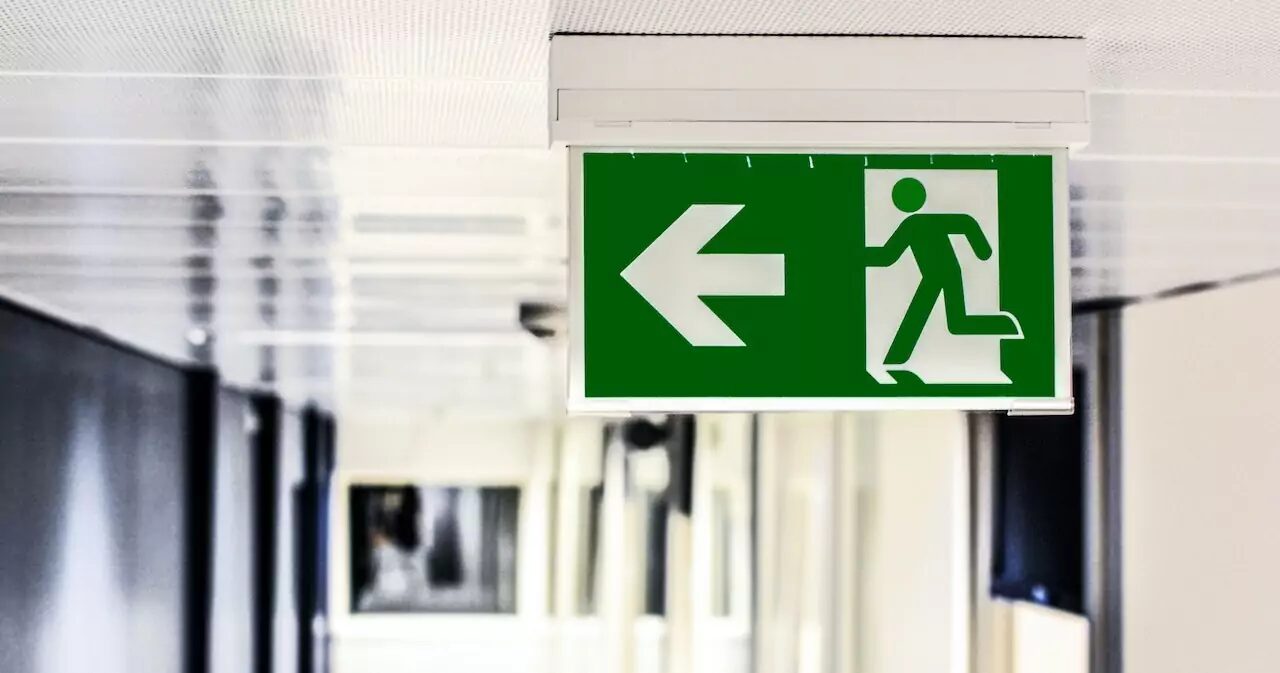
Material selection is arguably the most critical product manufacturing choice. It determines a product’s lifespan under everyday usage, its performance when stressed, and whether it will meet safety testing.
Hard plastics, as a whole, are a sought-after choice in industries due to their blend of functionality, durability, freedom of design, and visual appeal.
Whether used for consumer products, industrial parts, or medical equipment, every type of hard plastic has its own special properties that suit a particular purpose.
Below, we break down the eight types of hard plastic materials that engineers and designers rely on – each with niche strengths for specific challenges.
1. Acrylic
Acrylic, or polymethyl methacrylate (PMMA), delivers the transparency of glass without the fragility. Acrylic is known for its excellent optical clarity and resistance to UV radiation.
Many industries turn to this plastic for a robust, glass-like alternative, with its applications spanning from aquariums to display cases and automotive windows. It’s also a preferred choice for signage, lighting installations, and consumer electronics components. Through techniques like extrusion and injection molding, manufacturers turn acrylic into an extensive range of hard plastic products that deliver both structural integrity and refined aesthetics.
2. Polycarbonate
Polycarbonate balances transparency with high-impact resistance. Its capacity to withstand intense force suits safety-critical roles: bulletproof windows, riot shields, protective barriers in public spaces, or medical devices. For comparison, it absorbs impacts more effectively than standard glass or acrylic, though exact performance depends on the alloy grade and manufacturing method.
Despite its rigidity, polycarbonate molds cleanly under heat, enabling complex shapes like curved visors or optical lenses. A common tradeoff is surface vulnerability to abrasion, which manufacturers address with scratch-resistant coatings or composite blends (e.g., polycarbonate layered with acrylic).
This hard plastic retains structural integrity up to 140°C, making it suitable for automotive interiors, outdoor machinery components, and electrical enclosures. While alternatives exist, polycarbonate remains a default choice where optical clarity, heat resistance, and modifiable toughness intersect.
3. High-Density Polyethylene (HDPE)
HDPE is a strong yet lightweight plastic known for its resistance to corrosion, chemicals, and UV radiation. Owing to its versatility and affordability, you’ll find it in industrial pipe networks, chemical storage tanks, and safety gear where reliability can’t be compromised.
Its weatherproof traits make it a top pick among other types of plastic materials for harsh outdoor settings. You’ll see it in marine docks enduring saltwater spray, playground equipment surviving decades of sun, and irrigation systems.
4. Polyvinyl Chloride (PVC)
PVC’s reputation for durability and fire resistance makes it a staple in construction and industrial applications. While you may be familiar with its flexible form in cables and tubing, the rigid variant drives heavy-duty applications. It’s the backbone of industrial piping, window frames, and infrastructure where fire resistance and chemical stability are often non-negotiable.
Flame-retardant by nature, this hard plastic reduces fire risks in building materials, and its weather resistance keeps outdoor installations intact for a long time.
5. Acrylonitrile Butadiene Styrene (ABS)
ABS maintains a balance between being rigid and slightly flexible – it’s stiff enough to hold its shape and doesn’t crack easily, even when dropped or hit. It’s also resistant to chemical corrosion.
You’ll find ABS in electronics like keyboard switches and power tool casings, where its electrical insulation and chemical resistance keep components safe. That same toughness, paired with a smooth finish that holds pigments reliably, makes it crucial in making toys like LEGO bricks, musical instruments, and kitchen appliances.
In cars, this hard plastic balances practicality and safety: dashboard trim resists rattling, while interior panels cushion vibrations. And because it heats and cools quickly during injection molding processes, manufacturers mass-produce everything from vacuum cleaner shells to ergonomic tool grips.
6. Polytetrafluoroethylene (PTFE)
PTFE – better known by its brand name, Teflon – can handle scorching heat, icy cold, and even aggressive chemicals without degrading. It’s also renowned for its non-stick properties.
You’ll commonly find PTFE in two roles: protector and enabler. It coats factory pipe linings to contain corrosive acids, insulates sensitive electronics to prevent shorts, and keeps medical tools sterile with non-porous surfaces.
Beyond industry, it’s the reason why raincoats shed water easily and why high-performance ski wax minimizes drag for faster gliding. It is also frequently used in cookware.
What makes PTFE different from other types of plastic materials is its low friction and strong chemical resistance, which make it indispensable for seals, gaskets, and linings in harsh settings.
7. High-Impact Polystyrene (HIPS)
High-impact polystyrene (HIPS) combines cost-effectiveness with versatility. Its flexibility prevents cracking under stress, making it suitable for retail signs, toy packaging, and disposable utensils that bend without breaking. Its machinability and impact resistance make it ideal for a wide variety of industrial applications.
You can drill, sand, or paint it easily, which explains this hard plastic’s use in DIY projects and industrial applications like electronics trays. Printers choose HIPS for graphics that stay flat and precise, while manufacturers value its compatibility with thermoforming machines for FDA-approved food containers.
Replacing heavier materials like wood, metal, or other types of plastic materials with HIPS reduces shipping costs without compromising protection. For cosmetic displays, device packaging, or temporary displays, it provides durability and adaptability at a practical price point.
8. Acetal
Acetal, also known as polyoxymethylene (POM), thrives in high-performance engineering environments where durability matters. Its low-friction surface and rigid structure stay intact under stress, moisture, and repeated motion. Unlike metal, it isn’t susceptible to rust, squeaks, and greasy upkeep – ideal for zippers that glide smoothly, watch gears that keep ticking, or hinges on eyewear that survive daily wear.
You’ll see this hard plastic in medical inhalers delivering consistent doses, conveyor belts resisting oils in factories, and fuel pumps handling automotive heat. Its ability to reduce friction makes it a stealth star in bearings, gears, and fasteners, ensuring machinery runs cooler and quieter.
And when temperatures climb – up to 90°C – acetal holds its shape, rigidity, and strength. That’s why it works well in dishwashers, car engine components, and electrical components requiring excellent insulating properties.
Learn More at Polymershapes
At Polymershapes, we deliver solutions engineered for the fabrication challenges you face daily.
Each of these types of plastic materials offers unique properties that make them suitable for an enormous range of applications. From gears that need to glide to medical components requiring precision, the right type of plastic defines your project’s success. As a leading hard plastics fabrication company, Polymershapes understands the potential of these materials. That’s why we’re committed to delivering high-quality, durable, and versatile plastic materials for your fabrication and material processing needs. Learn more by contacting our highly trained and knowledgeable sales and customer service team.
If you have a project that requires these types of hard plastics, contact our expert team or request a quote to get started.